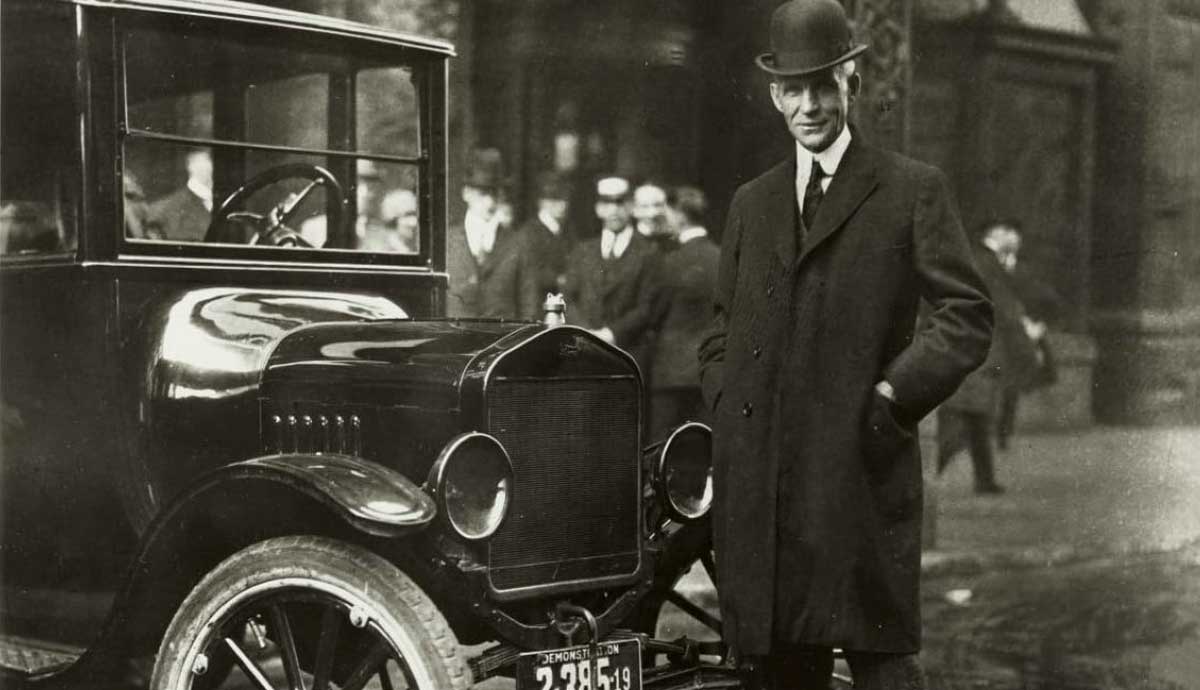
Henry Ford is largely responsible for kickstarting a new form of mass production with the moving assembly line. With increased production and skyrocketing sales, Ford mass-produced his famous Model T automobiles. Buying a new car was no longer a luxury of the wealthy but a standard practice of the middle class. Wages of workers were increased, and workdays were shortened. Ford established a new mass production system that influenced the future of manufacturing and brought more attention to a consumer-centered lifestyle.
Early Life of Henry Ford
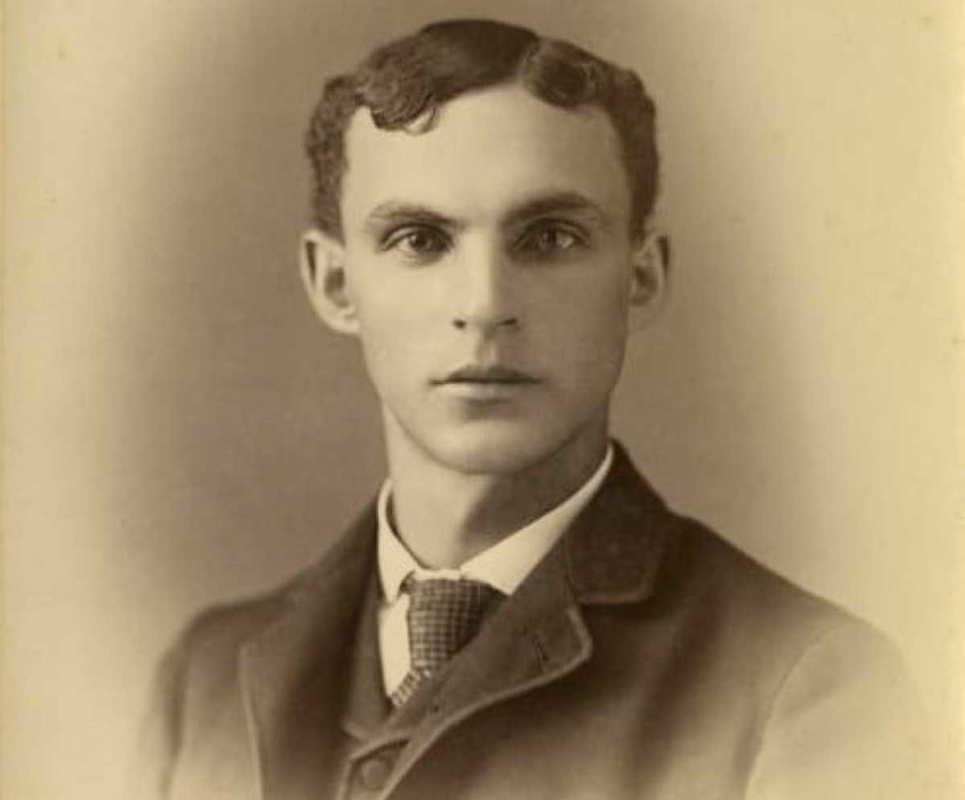
Henry Ford became interested in mechanics and the operations of machinery at a young age. Ford was born on July 30, 1863 and raised on a farm in Springwells Township located in Wayne County, Michigan. He was one of six children. By the time Ford had turned 12 years old, he had a small shop set up where he spent most of his time tinkering with machinery. Three years later, he managed to create his own steam engine. One of Ford’s first jobs was as a machinist’s apprentice at James F. Flower and Brothers, located in Detroit. He worked with brass valves designed for milling machines. He got to explore more of his interests in machinery in this position at a rate of $2.50 per week.
While working as a machinist’s apprentice, he was also hired as an apprentice for the Detroit Dry Dock Company. He spent three years working as an apprentice before moving on to steam engine repair work. Ford found a job at the Edison Illuminating Company in Detroit in July 1891. After two years of employment, he was promoted to chief engineer. The Edison Illuminating Company was fairly new at the time; it was established by Thomas Edison in 1880 after he had just invented the incandescent lamp, or light bulb, a year prior. Ford met Edison, who became somewhat of a mentor and lifelong friend.
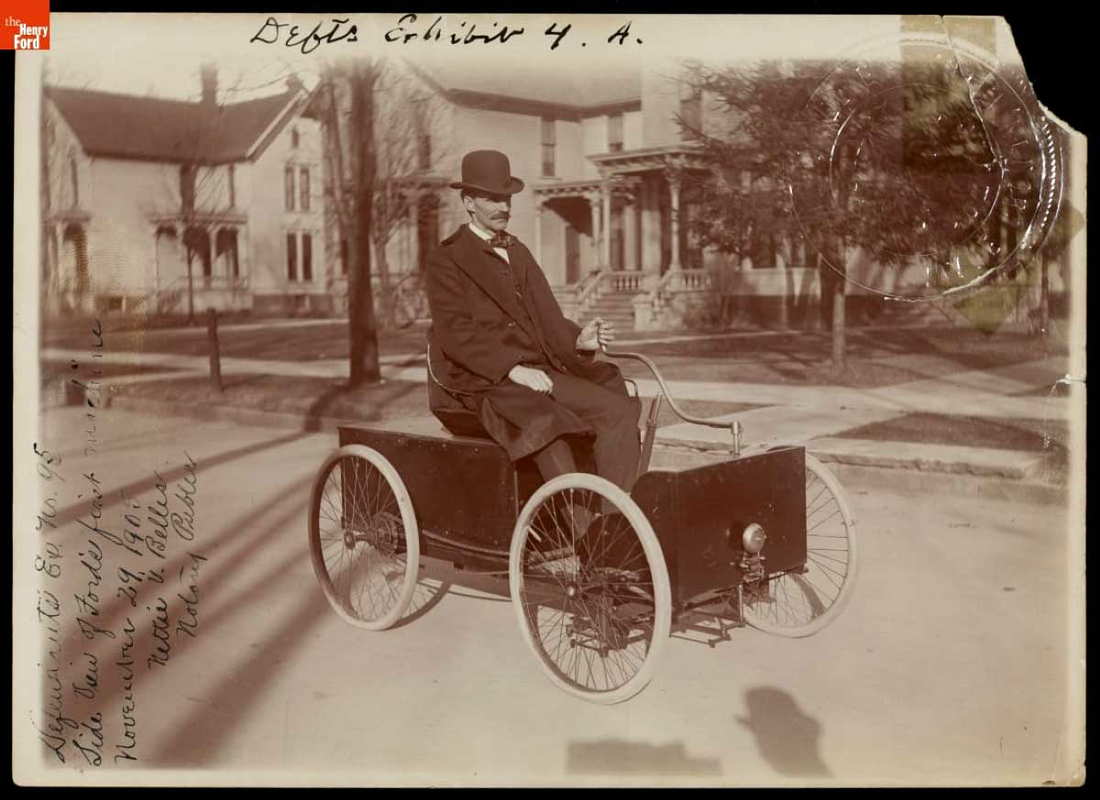
While working as a chief engineer, Ford began to explore his interests in automobiles on the side. He created his first engine at his home in Detroit in the early 1890s. Ford liked to improve upon his creations and constructed a new and improved engine by 1896. The engine was used in the very first automobile he created, known as the Quadricycle. It consisted of four bicycle wheels, one seat, a frame, and a gas-powered engine. The transmission was made of a leather belt and chain drive. A long, curvy rod with a small handle was used to steer the vehicle. Ford sold it the same year for $200 and used his profits to begin working on his next automobile project. He eventually bought the Quadricycle back almost a decade later.
In the late summer of 1899, Ford made his first attempt at starting his own automobile business. He quit his job at the Edison Illuminating Company and created the Detroit Automobile Company. This business venture ultimately failed, ending in bankruptcy about a year and a half later. He attempted another automobile business venture in 1901 by founding the Henry Ford Company. He left the company just months later, in 1902, which later turned into the Cadillac Motor Car Company.
Transportation in the Early 20th Century
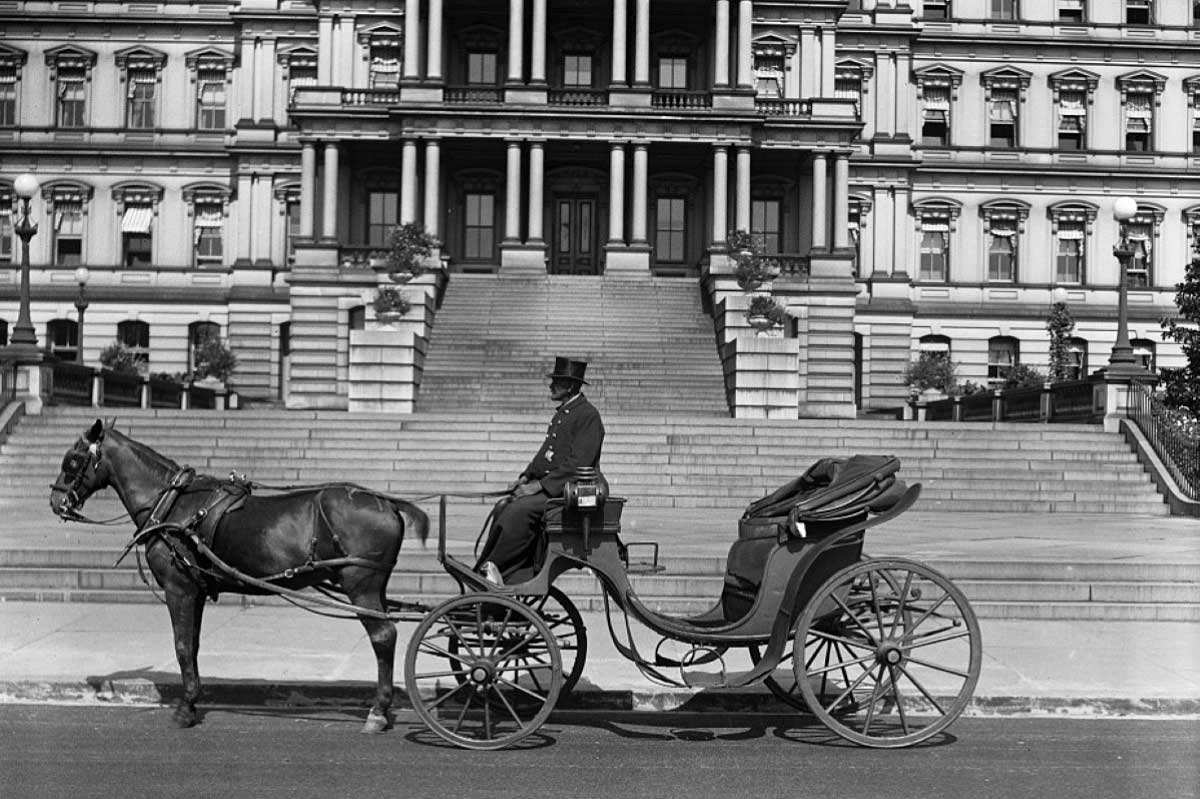
Different types of automobile inventions had been around since the 18th century. Steam and electric-powered modes of transportation came before gas. Karl Benz is often associated with inventing the first “true automobile,” which was powered by gasoline using an internal combustion engine. He created the vehicle in 1885, and it was patented in 1886. Frank and Charles Duryea established the Duryea Motor Wagon Company, the first automobile manufacturer in the US.
The most common way to get around in the early 20th century was by horse-drawn carriages. Although cars were being produced, most people couldn’t afford them. It was considered a luxury item. Even the factory workers who were creating the automobiles weren’t earning high enough wages to afford the convenience of an automobile. The American railroad system in the early 1900s offered a quicker mode of transportation. It also helped to connect people and places at longer distances.
The invention of the gas-powered automobile was by no means new by the time Henry Ford came into the industry. However, he created a system that other automobile manufacturers didn’t have: he was able to establish an automobile assembly line that changed the way goods made their way through production. The transformation to a faster way of production helped influence how the automobile became a part of the daily lives of most people in America.
Beginnings of the Ford Motor Company
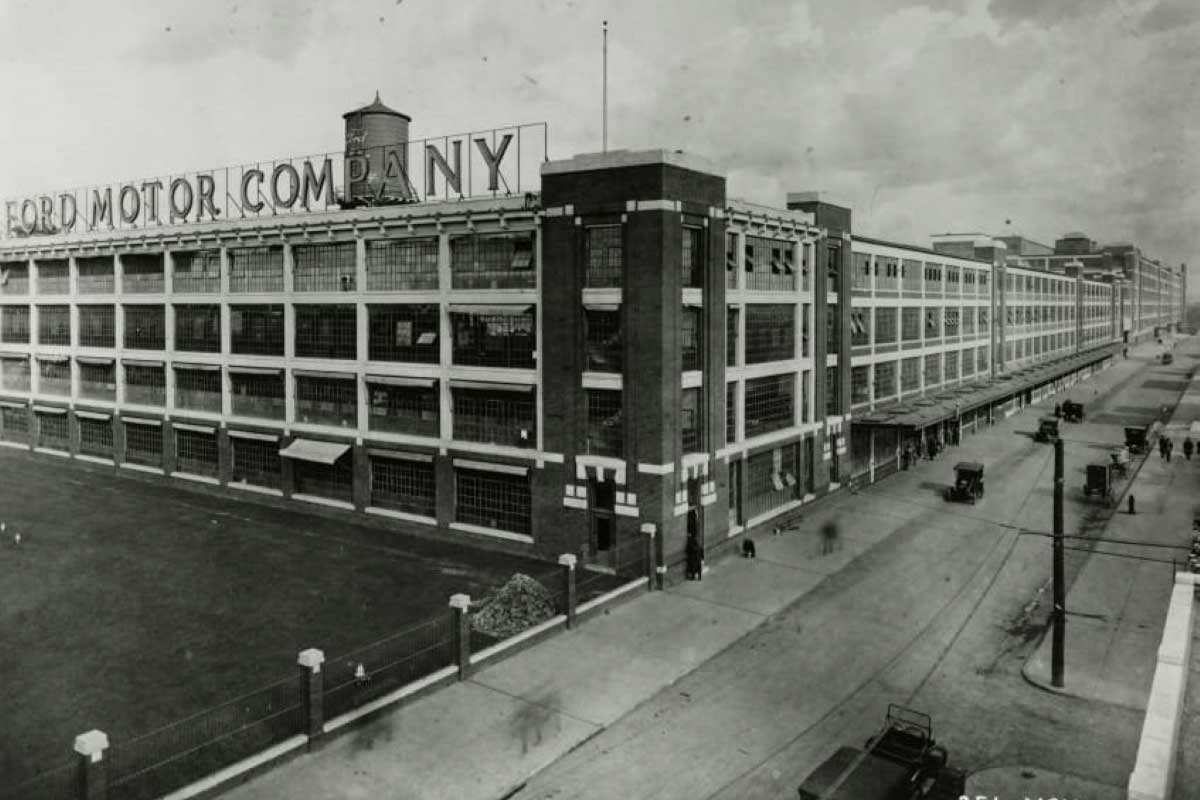
After Ford dropped his second automobile business venture, he decided to organize another company with several other investors. A total of $28,000 was initially invested in establishing the Ford Motor Company in 1903; Ford owned 25.5% of the stock. One of his partners was Alexander Malcomson, a businessman and the largest coal dealer in Detroit. In the company’s first five years, Ford created nine different automobile models. The Ford Model A was the first vehicle sold in July 1903. The Model N was the most successful of the group and helped Ford gain popularity and increase sales.
The first Model T was introduced in October 1908 and manufactured in one of the first Ford Motor facilities, the Ford Piquette Avenue Plant. It quickly became the most successful Ford model produced and was one of the best-selling vehicles of the time. One of the main manufacturing plants for the Ford Motor Company was the Ford Highland Park Plant in Michigan. It was designed by American industrial architect Albert Kahn. The plant officially opened in January 1910 and became the first location to operate the automobile moving assembly line.
The Automobile Assembly Line & Mass Production of the Model T
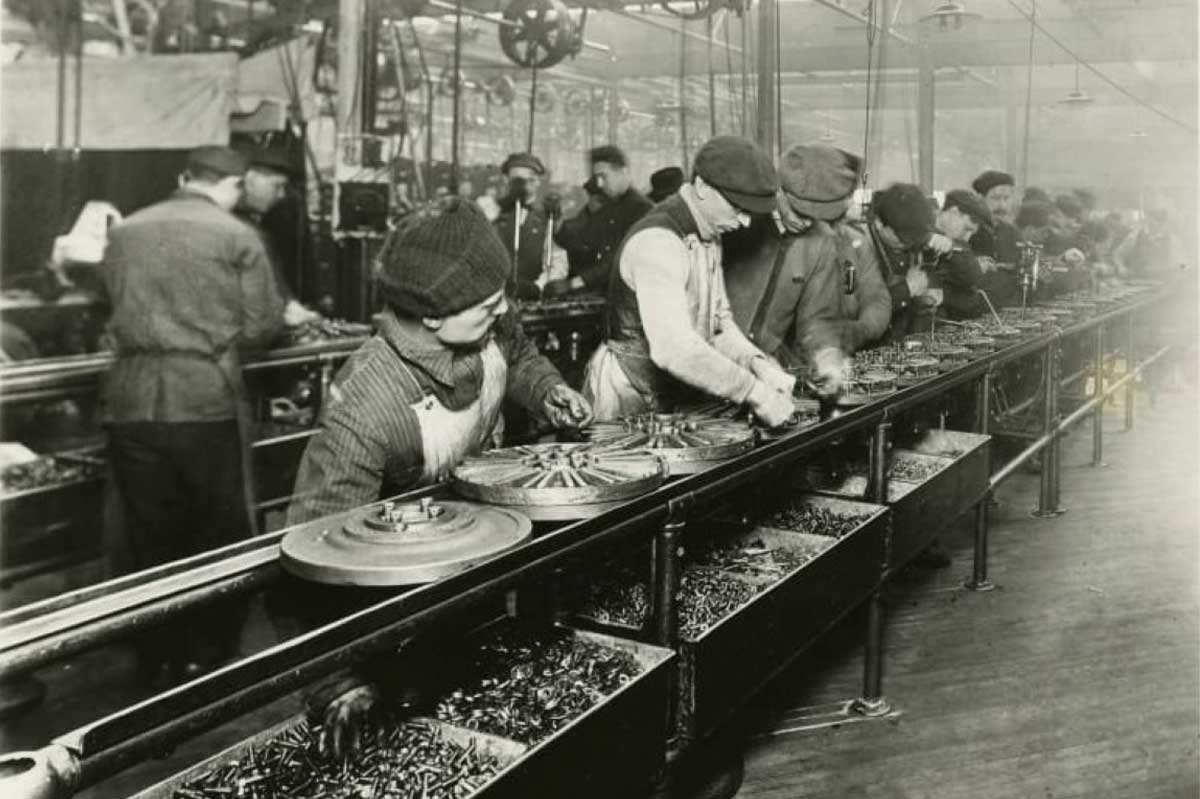
The biggest transformation to the automobile industry and manufacturing as a whole came with the introduction of the moving assembly line. Ford is often mistaken for the inventor of the assembly line; however, Ransom Olds was one of the early automobile manufacturing pioneers who mass-produced automobiles in the US. At the time the Ford Motor Company was founded, Old’s company Olds Motor Works was one of the largest automobile manufacturers in the nation.
Ford made improvements to Olds’ stationary assembly line, and his innovations led to the moving assembly line. The conveyor belt was a feature of the assembly line that also wasn’t completely new. Conveyor belts were used in manufacturing plants in other industries. After a few failed attempts, however, Ford managed to create an assembly line that moved automobile parts down to lines of workers on a conveyor belt system. The moving assembly line was up and running in the Highland Park plant by 1913. It allowed for the workers to be assigned just one or two tasks. This differed from common manufacturing methods that had workers learning how to complete all tasks to build a product rather than specialize in one.
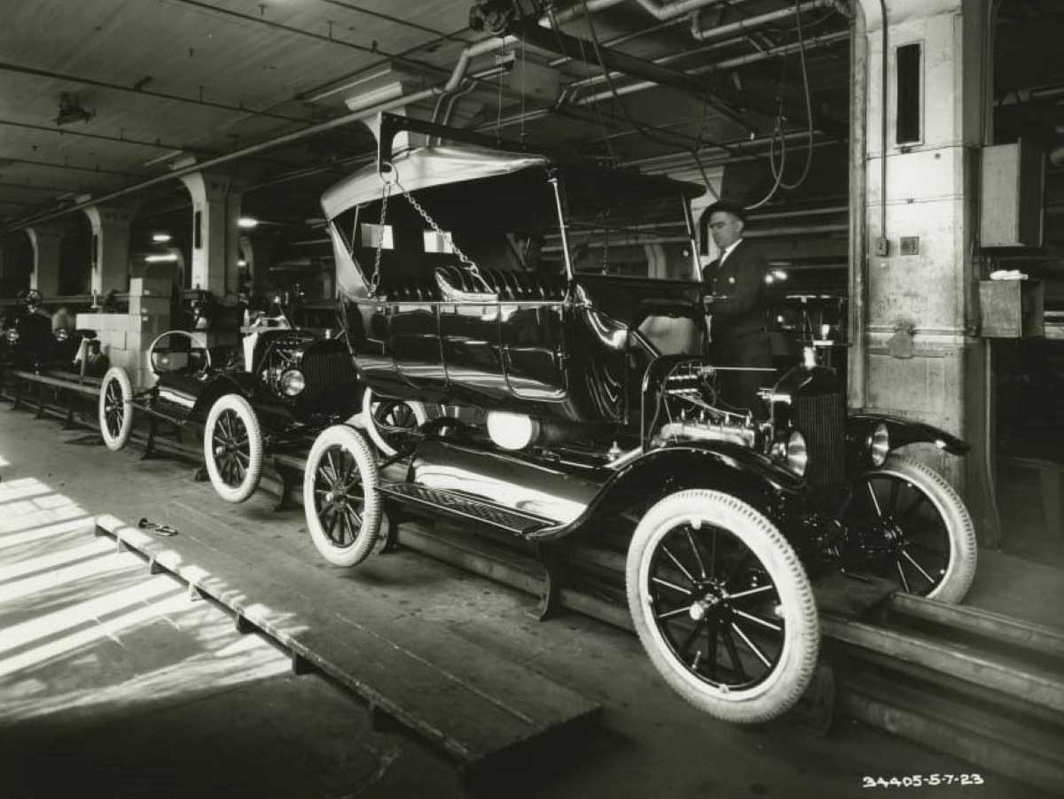
The time it took for a new Model T to be assembled using the moving assembly line system reduced dramatically. Model T’s initially took about 12 hours to complete. The new system reduced this time to just 93 minutes. Since the Model T was rolling out of the plant at a much faster rate, it helped reduce the cost. The Model T was considered one of the most affordable cars for the middle class at the time. Owning an automobile was no longer thought of as a luxurious product strictly for the elite. The price of a new Model T in 1924 had dropped to $260, almost $600 less than the cost 15 years prior. More than 15 million Model T cars were produced from the time they were introduced to the time they were discontinued in 1927.
The assembly line wasn’t always rewarding to Ford. It cost him workers, as many found the job boring because they concentrated on one or two tasks repeatedly. Many workers went to work for competitors. In response, Ford devised a plan to raise his workers’ wages to five dollars per day. The increase was almost double what the workers were making before, and as a result, thousands of workers put in an application to work at the Ford Motor Company. Along with a raise, Ford also implemented a new eight-hour workday. His wages and workday hours were unlike anything else that other manufacturers were offering.
How Henry Ford Transformed the Workday & Manufacturing System
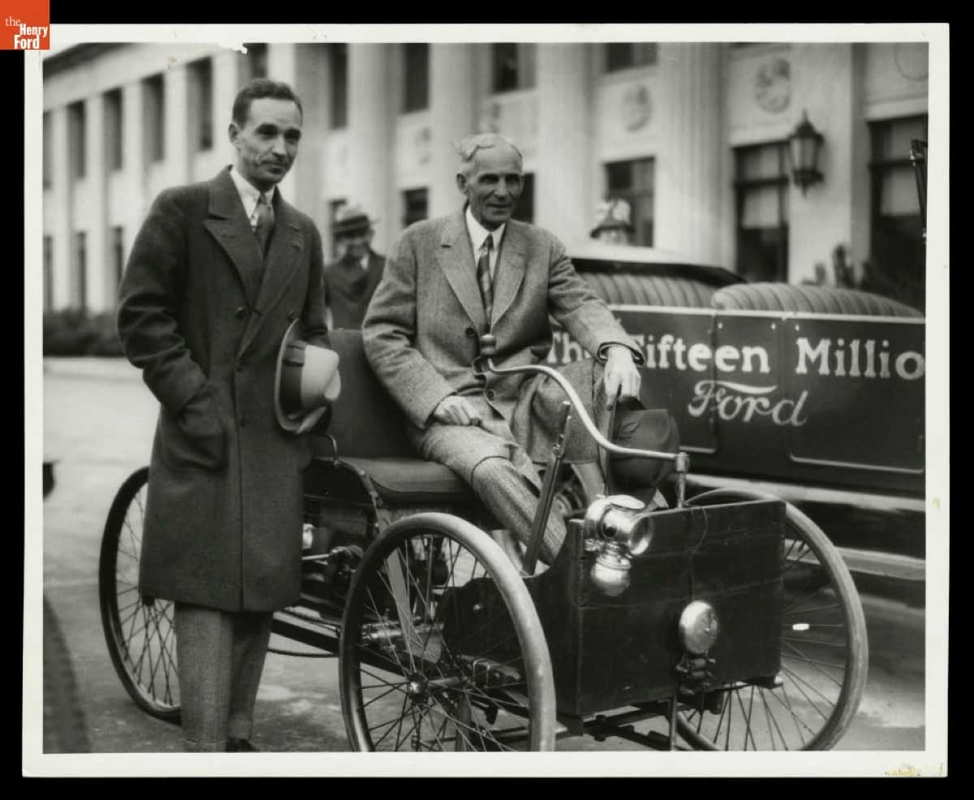
Henry Ford’s introduction of a wage bump and the eight-hour workday encouraged other manufacturers to do the same. Other businesses were forced to compete with companies offering more to workers. The formation of labor unions also forced business owners to compromise with workers’ wants and needs. Ford also had to deal with a union strike for Ford Motor Company workers. They wanted better working conditions. Ford refused to compromise at first, but he eventually came around to giving them what they asked for and more.
Some of Ford’s business ideas weren’t the best. In 1927, Ford attempted to supply his own rubber and set up plantations in Brazil. It was called Fordlandia, but after a number of hardships and issues, it ended up as a failed business move.
The ideas that Ford had for mass production caused the current state of the American Industrial Revolution to shift. The push to meet product demands created harsh working conditions and long hours for pitiful wages as industrialization was building up steam. Moving assembly lines allowed products to be created faster and took some pressure off workers. It set the foundation for a mass production system, which soon led to the rise of consumerism.
Ford influenced the rise of wages for many industries. Demand for higher wages was becoming increasingly common, and companies risked closing down and losing workers for weeks if an agreement wasn’t reached. The mass production of the Model T made the automobile affordable for the middle class. Other automobile companies raced to make better cars also at lower prices to compete with Ford. It bridged some of the gaps in the class system that separated the elites from the middle and working classes.